AISI 1020 AISI 1018 Low Medium High Carbon Steel Sheet Metal Hot Rolled
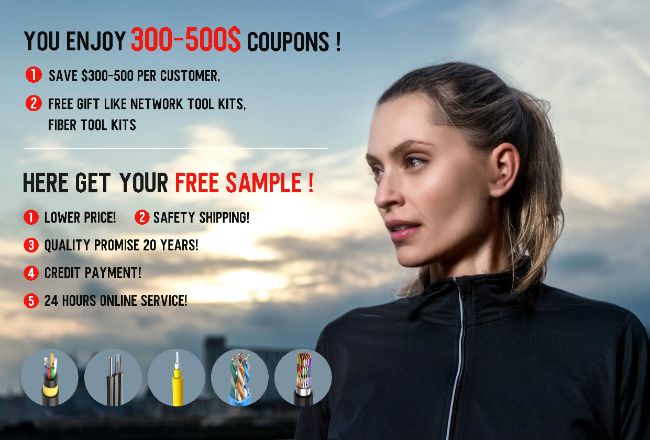
Contact me for free samples and coupons.
Whatsapp:0086 18588475571
Wechat: 0086 18588475571
Skype: sales10@aixton.com
If you have any concern, we provide 24-hour online help.
xProduct Name | Carbon Steel Plate | Delivery Conditon | HR,CR,AR,Q+T,N+T,N,TMCP,UT,Z Direction |
---|---|---|---|
Thickness | 3mm~3000mm | Width | 1500mm/2200mm/2500mm |
Length | 6000-12000mm | ||
High Light | 3000mm 1020 carbon steel sheet,12000mm aisi 1020 steel sheet,6000mm aisi 1018 sheet |
Mild steel plates, also known as plain-carbon steel and low-carbon steel, are extremely strong due to the low amounts of carbon present inside them. The carbon amount typically found in mild steel range from 0.05%-0.25% by weight. Here, less carbon means that mild steel is more ductile, malleable, weldable, and machinable than carbon and other steels. Because of its high strength and malleability, MS plates are a popular steel choice for the construction of pipelines and everyday products. Moreover, the ease of shaping and welding MS plates makes them a desirable material for producing products in the consumer industry.
High Ductility
Robust Construction
Dimensionally Stable
Fine Surface Finish
Durable
Abrasion Resistant
Light weight
AISI 1020 Steel is low hardenability and low tensile carbon steel carbon steel. And its Brinell hardness of 119 – 235 and tensile strength of 410-790 MPa. It is normally used in turned and polished or cold drawn condition. AISI 1020 steel ( JIS S20C steel) is resistant to induction hardening or flame hardening due to its low carbon content.
EQUIVALENT GRADE OF ASTM 1020
Europe EN |
Germany DIN |
China GB |
Japan JIS |
C22E | CK22/1.1151 | 20 | S20C |
CHEMICAL COMPOSITION: AISI 1018 VS AISI 1020
Element | C | Mn | Fe | P | S |
AISI 1018 | 0.14~0.20% | 0.60~0.90% | 98.81~99.26% | 0.040% | 0.050% |
AISI 1020 | 0.17~0.23% | 0.30~0.60% | 99.08~99.53% | 0.040% | 0.050% |
HEAT TREATMENT
It can be heat treated at the following temperatures:
- Normalizing at 899°C – 954°C (1650°F-1750°F)
- Annealing at 843°C – 871°C (1550°F-1600°F)
- Stress relieving at 677°C – 927°C (1250°F-1700°F)
- Carburizing at 899°C – 927°C (1650°F-1700°F)
- Hardening at 788°C – 816°C (1450°F-1500°F)