201 202 410 Astm Stainless Steel Strip Polished 1mm 2mm 3mm
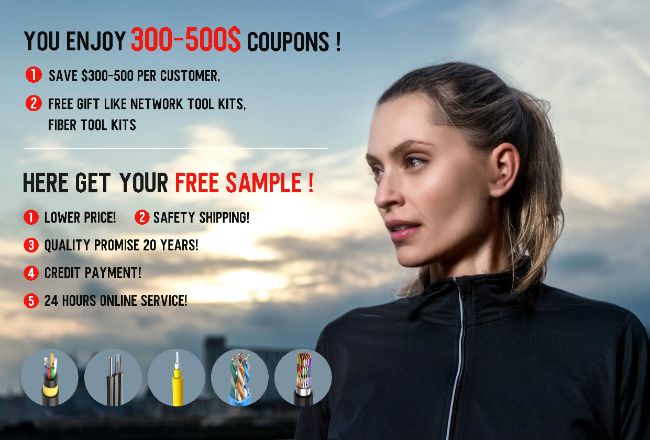
Contact me for free samples and coupons.
Whatsapp:0086 18588475571
Wechat: 0086 18588475571
Skype: sales10@aixton.com
If you have any concern, we provide 24-hour online help.
xProduct Name | Stainless Steel Coils/Strips | Type | Cold Rolled,Hot Rolled |
---|---|---|---|
Surface | No.1,2D,2B,BA,No.4,8k,Tempered | Thickness | 0.4mm~6mm |
High Light | 201 stainless steel strip,202 stainless steel strip,410 stainless steel strip |
Grade 410 Stainless Steel Coils/Strips
What Is Stainless Steel Strips Surface Finish?
Stainless steel has become a widely used metal material for its excellent corrosion resistance, good mechanical properties and processing properties.
Through different processing methods of cold rolling and surface reprocessing after cold rolling, the surface finish of stainless steel can have different types.
The surface processing of stainless steel strips have NO.1, 2B, No. 4, HL, No. 6, No. 8, BA, TR hard, Rerolled bright 2H, polishing bright and other surface finishes, etc.
400 SERIES STAINLESS STEEL
The 400 series group of stainless steels typically have an 11% chromium and 1% manganese increase, above the 300 series group. This stainless steel series tends to be susceptible to rust and corrosion under some conditions although heat-treating will harden them. The 400 series of stainless steels have a higher carbon content, giving it a martensitic crystalline structure that provides the end product with high-strength and high-wear resistance. The 400 series steels tend to be used in agricultural equipment, gas turbine exhaust silencers, hardware, motor shafts, and more.
Type 410 is hardenable, straight-chromium stainless steels which combine superior wear resistance of high carbon alloys with the excellent corrosion resistance of chromium stainless steels. Oil quenching these alloys from temperatures between 1800°F to 1950°F (982-1066°C) produces the highest strength and/or wear resistance as well as corrosion resistance. Type 410 alloy is used where strength, hardness, and/or wear resistance must be combined with corrosion resistance
CHEMICAL COMPOSITION
Element | C | Mn | Cr | Ni | P | S | Si |
409 | 0.03% | 1.00% | 10.5~11.7% | 0.50% | 0.04% | 0.02% | 1.00% |
410 | 0.08~0.15% | 1.00% | 11.5~13.5% | 0.75% | 0.04% | 0.03% | 1.00% |
420 | 0.15% | 1.00% | 12.0~14.0% | - | 0.04% | 0.03% | 1.00% |
430 | 0.12% | 1.00% | 16.0~18.0% | 0.75% | 0.04% | 0.03% | 1.00% |
MECHANICAL PROPERTIES
Grade |
Tensile Strength (MPa) Min |
Yield Strength 0.2% proof (MPa) Min |
Elongation (%in 50mm) Min |
Rockwell B(HRB) Max |
410 |
510
|
290 | 34 | 82-96 |
410 COMMON APPLICATIONS
The typical applications of grade 410 stainless steels are listed below:
- Bolts, screws, bushings and nuts.
- Petroleum fractionating structures.
- Shafts, pumps and valves.
- Mine ladder rungs.
- Gas turbines